Introduction
Overhead power lines are a critical component of our electrical infrastructure, providing the necessary transmission of electricity across vast distances to power homes, businesses, and industries. However, these power lines are constantly exposed to environmental elements that can lead to corrosion and degradation over time. Corrosion of overhead power lines can result in costly repairs, power outages, and safety hazards. Therefore, it is essential to implement effective corrosion prevention measures to ensure the reliability and longevity of these vital structures.
In this comprehensive guide, we will explore the various factors that contribute to corrosion in overhead power lines, the different types of corrosion that can occur, and the most effective strategies for preventing corrosion and maintaining the integrity of these critical infrastructure assets.
Factors Contributing to Corrosion in Overhead Power Lines
Corrosion in overhead power lines can be caused by a combination of factors, including environmental conditions, material composition, and design considerations. Understanding these factors is crucial in developing an effective corrosion prevention plan.
1. Environmental Conditions
Environmental conditions play a significant role in the corrosion of overhead power lines. Factors such as humidity, temperature fluctuations, exposure to saltwater or industrial pollutants, and the presence of corrosive gases can accelerate the corrosion process. For example, coastal areas with high salt content in the air are more prone to corrosion due to the corrosive nature of salt.
2. Material Composition
The material composition of overhead power lines also influences their susceptibility to corrosion. Common materials used in power line construction include steel, aluminum, and copper. Each material has its own corrosion properties, with steel being more prone to rusting, while aluminum and copper are more resistant to corrosion. However, even corrosion-resistant materials can degrade over time when exposed to harsh environmental conditions.
3. Design Considerations
The design of overhead power lines can impact their vulnerability to corrosion. Factors such as the presence of sharp edges or crevices where moisture can accumulate, inadequate protective coatings, and poor maintenance practices can all contribute to the accelerated corrosion of power line structures. Proper design considerations, including the use of corrosion-resistant materials, effective coatings, and regular inspections, are essential in preventing corrosion in overhead power lines.
Types of Corrosion in Overhead Power Lines
Corrosion in overhead power lines can manifest in various forms, each with its own characteristics and impacts on the structural integrity of the power line. Understanding the different types of corrosion is essential in developing targeted prevention strategies.
1. Galvanic Corrosion
Galvanic corrosion occurs when two dissimilar metals are in contact with each other in the presence of an electrolyte, such as moisture. This can happen in overhead power lines where different metals are used in construction, leading to accelerated corrosion at the interface between the metals. Galvanic corrosion can weaken the structural integrity of the power line and result in premature failure if not addressed promptly.
2. Pitting Corrosion
Pitting corrosion is a localized form of corrosion that results in the formation of small pits or craters on the surface of the metal. This type of corrosion is particularly insidious as it can be difficult to detect visually, leading to significant structural damage before it is identified. Pitting corrosion in overhead power lines can compromise the structural integrity of the line and increase the risk of catastrophic failure.
3. Crevice Corrosion
Crevice corrosion occurs in confined spaces or crevices where moisture is trapped and unable to evaporate. This type of corrosion is common in areas where power line components are joined or fastened together, creating potential sites for crevice corrosion to develop. Crevice corrosion can weaken the connections between power line components and increase the risk of structural failure.
4. Atmospheric Corrosion
Atmospheric corrosion is caused by exposure to environmental elements such as moisture, oxygen, and pollutants in the air. Over time, these factors can react with the metal surface, leading to the formation of corrosion products that weaken the structural integrity of the power line. Atmospheric corrosion is a common form of corrosion in overhead power lines, especially in areas with high humidity or industrial pollution.
Prevention Strategies for Corrosion in Overhead Power Lines
Preventing corrosion in overhead power lines requires a comprehensive approach that addresses the various factors contributing to corrosion and employs a combination of protective measures to safeguard the structural integrity of the power line. The following strategies can help mitigate the risk of corrosion and extend the lifespan of overhead power lines:
1. Material Selection
Choosing the right materials for overhead power line construction is critical in preventing corrosion. Opting for corrosion-resistant materials such as aluminum or copper can help minimize the risk of corrosion and extend the lifespan of the power line. Additionally, selecting materials with protective coatings or finishes can provide an extra layer of defense against environmental factors.
2. Protective Coatings
Applying protective coatings to power line structures is an effective way to prevent corrosion and extend their service life. Protective coatings act as a barrier between the metal surface and the corrosive environment, preventing moisture and other corrosive agents from reaching the underlying metal. Regular inspection and maintenance of protective coatings are essential to ensure their continued effectiveness in preventing corrosion.
3. Cathodic Protection
Cathodic protection is a corrosion prevention technique that involves applying a direct current to the metal surface to counteract the electrochemical reactions that cause corrosion. This method is particularly effective in preventing galvanic corrosion in overhead power lines where dissimilar metals are in contact. Implementing a cathodic protection system can help mitigate the risk of corrosion and extend the lifespan of power line structures.
4. Regular Inspections and Maintenance
Regular inspections and maintenance are essential components of any corrosion prevention plan for overhead power lines. Conducting visual inspections to identify signs of corrosion, such as rust, pitting, or discoloration, can help detect corrosion early and prevent further damage. Implementing a proactive maintenance schedule to address any corrosion issues promptly can help extend the lifespan of power line structures and prevent costly repairs.
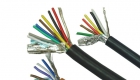
5. Environmental Monitoring
Monitoring environmental conditions around overhead power lines can help identify potential corrosion risks and inform preventive measures. Installing environmental sensors to track factors such as humidity, temperature, and pollution levels can provide valuable data to assess the corrosion risk and implement targeted prevention strategies. By monitoring environmental conditions, operators can proactively address corrosion risks and protect the structural integrity of power lines.
6. Design Considerations
Incorporating corrosion-resistant design features into overhead power line structures can help minimize the risk of corrosion and extend their service life. Design considerations such as avoiding sharp edges or crevices where moisture can accumulate, using corrosion-resistant materials, and implementing effective drainage systems can all contribute to preventing corrosion in power line structures. By addressing corrosion risks at the design stage, operators can reduce maintenance costs and ensure the long-term integrity of overhead power lines.
Related Site in overhead power lines poses a significant risk to the reliability and safety of our electrical infrastructure. By understanding the factors that contribute to corrosion, recognizing the different types of corrosion that can occur, and implementing targeted prevention strategies, operators can effectively protect overhead power lines from corrosion and ensure their long-term integrity. By selecting corrosion-resistant materials, applying protective coatings, implementing cathodic protection systems, conducting regular inspections, monitoring environmental conditions, and considering design considerations, operators can mitigate the risk of corrosion and extend the lifespan of overhead power lines. Ultimately, investing in corrosion prevention measures is essential in safeguarding the reliability of our electrical grid and ensuring the uninterrupted transmission of electricity to power our communities.